Good Manufacturing Practice (GMP) Facility
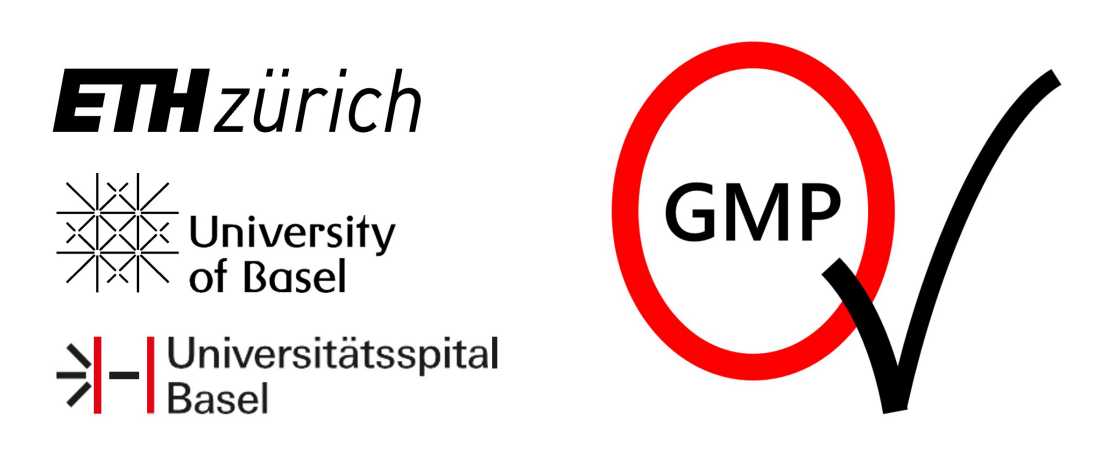
The GMP (Good Manufacturing Practice) Facility ETH-Unibas-USB, currently set up and hosted by D-BSSE in its new building, is an ETH technology platform shared with University of Basel and University Hospital Basel (operational by the end of 2024). In our academic setting, the GMP platform objective is to provide an environment compliant with the regulatory requirements, which enables researchers to manufacture their gene, cell, and tissue therapy products (Advance Therapeutic Medicinal Product, ATMP) for use in human clinical trials. As such, a GMP platform is a key component of translational research.
The facility equipment enables a range of biological manufacturing processes; from small patient-based products to large bioreactor-produced batches. The facility is not a contract manufacturing organisation, but an open platform in which external project teams are trained, supervised and supported by the facility core team to accomplish GMP-compliant manufacturing of ATMPs for clinical trials. Project teams, of academic researchers and clinical collaborators, are responsible for manufacturing and for most of the testing and documentation tasks. The final batch release to the sponsor (for use in clinical trial) remain under the responsibility of the “Qualified Person” or “Responsible Person”(QP or RP) from the core team. Third parties such as external academic partners or private entities will be able to access the facility based on availability.
Among the pillars of GMP are risk-based analysis, validation and control of every aspect of the environment, equipment, material, procedures and personnel employed in the manufacturing process. To support this comprehensive approach and its intensive documentation activity, the platform is endowed with an electronic Quality/Document Management System including audit trail and electronic signature.
The GMP Platform consists of a manufacturing facility (floor B) and a quality control (floor C) facility.
The manufacturing facility (400 m2) on floor B of the BSS building, comprises three manufacturing suites. Each suite is divided into zones of increasing asepsis requirements: a large class C room adjacent to a class B room with a class A area that enables work with open product. The suites are surrounded by class D areas for microbiological monitoring, storage, and media preparation. These different zones are connected by air locks for protected passage of personnel and material.
Dr. Paul Zajac
Facility Head
(also Quality Assurance Manager and Qualified Person)
E-mail: paul.zajac@bsse.ethz.ch
Telephone: external page +41 61 387 34 54
Dr. Anita Ankli
Quality Control Manager
E-mail: anita.ankli@bsse.ethz.ch
Marcus Bicker
Quality Specialist
E-mail: marcus.bicker@bsse.ethz.ch